Chez EDIBON, nous sommes engagés à renforcer les compétences comme pilier stratégique pour la compétitivité et le bien-être social de l'Union européenne. Une formation adéquate renforce non seulement l'économie, mais permet également aux individus de participer pleinement à la société et à la...
0
Sélection
/
Vide
Votre sélection
Il n'y a plus d'articles dans votre sélection
AE-PLC-FMS3 Système de Fabrication Flexible de Transport, Assemblage, Sélection (Matériau et Couleur) et Stockage
SYSTEMES INNOVANTS
The Flexible Manufacturing System for Transport, Assembly, Selection (Material and Color), and Storage, "AE-PLC-FMS3", designed by EDIBON, enables the study and practice of an automated production cycle consisting of 5 distinct workstations. This system integrates all the mentioned workstations, as well as an additional feeding station.
NOUVELLES LIÉES
Description Générale
The Flexible Manufacturing System for Transport, Assembly, Selection (Material and Color), and Storage, "AE-PLC-FMS3", is a highly adaptable and configurable system designed for the study and application of advanced automation principles within the context of Industry 4.0 and Industry 5.0. This unit integrates key technologies such as automated control, inter-device networking through smart networks, PLC programming of assembly lines, and real-time data analysis, allowing users to explore the capabilities of digitized and connected manufacturing that characterize the Fourth Industrial Revolution and pave the way for the Fifth Industrial Revolution.
It consists of five interconnected stations that perform specific tasks related to feeding, transport, assembly, sorting (dimension, material, and color), screwing, and parts storage. Each of these workstations requires its own PLC from the selected brand (PANASONIC, SIEMENS, ALLEN BRADLEY, MITSUBISHI and/or OMRON), allowing users to explore how advanced control and production concepts are applied in an automated manufacturing line. The workflow is coordinated by a central PLC system (from the same brand chosen for the stations) and an Ethernet network, making the "AE-PLC-FMS3" a comprehensive learning resource for those interested in automation engineering and flexible manufacturing.
The included workstations are:
- Part Feeding Workstation, "AE-PLC-A": Initiates the cycle by moving base parts from the waiting position onto the conveyor belt.
- Linear Transport Workstation, "AE-PLC-T": Receives parts from the storage station and positions them for transfer to the next station.
- Mounting Workstation "AE-PLC-M": Adds a second part to the base, verifying dimensions before proceeding.
- Rotary Table Workstation: Feeding, Quality Control, and Assembly (material and color study), "AE-PLC-MR2": Checks the part’s material and color for quality.
- Storage Workstation, "AE-PLC-AL": Picks up the base parts with an automatic handler and places them in the designated storage area.
The system allows students and instructors to delve into fundamental concepts of industrial automation. Through its use, students acquire practical skills in designing and operating automated systems, gaining a deep understanding of the coordinated work across the various workstations of a real production line. This configurable system has been carefully designed so that each of its workstations performs specific functions that simulate real industrial processes.
The recommended Automation System Simulation Software, "AE-AS," enables the simulation of industrial processes in both 2D and 3D, providing full control and supervision, allowing users to safely experiment with automation software in a protected environment.
Des exercices et pratiques guidées
EXERCICES GUIDÉS INCLUS DANS LE MANUEL
Practical possibilities to be done with the Flexible Manufacturing System for Transport, Assembly, Selection (Material and Color), and Storage (AE-PLC-FMS3):
- Introduction to flexible manufacturing system (FMS).
- Introduction to pneumatics and electro-pneumatics.
- Introduction to vacuum technology.
- Study of the sensor detection.
- Testing the digital inputs and outputs of the automatic system through a PLC.
- Modify manufacturing parameters through the PLC.
- Configuration of a pneumatic application.
- Introduction to the Human-machine interface systems (HMI).
- Study of an automatic control of an industrial system.
- Control of the flexible manufacturing system through a central PLC in an Ethernet network with local PLC in each workstation.
- Manage the flexible manufacturing system through the HMI device.
Practical possibilities to be done with the workstation alone:- Feeding Workstation for Pieces (AE-PLC-A).
- Manual control of a Feeding system.
- Automatic control of a Feeding system.
- Change the parameters of the Feeding process.
- Optimize the process time.
- Study and analysis of the faults inserted in the process with the fault generation module.
- Linear Transport Workstation (AE-PLC-T).
- Manual control of a transporting system.
- Automatic control of a transporting system.
- Change parameters of a transporting process.
- Optimize the process time.
- Study and analysis of the faults inserted in the process with the fault generation module.
- Mounting Workstation (AE-PLC-M).
- Manual control of a mounting system.
- Automatic control of a mounting system.
- Change the parameters of the mounting process.
- Optimization of the process time.
- Study and analysis of the faults inserted in the process with the fault generation module.
- Rotary Table Workstation: Feeding, Quality Control, and Assembly (material and color study) (AE-PLC-MR2).
- Manual control of the rotary table system.
- Manual control of the quality control and drilling process on a rotary table.
- Automatic control of the rotary table system.
- Automatic control of the quality control and drilling process on a rotary table.
- Change the parameters of the rotary table process.
- Optimize the process time.
- Study and analysis of the faults inserted in the process with the fault generation module.
- Storage Workstation (AE-PLC-AL).
- Manual control of a storing system.
- Automatic control of a storing system.
- Change the parameters of the storing process.
- Optimize the process time.
- Study and analysis of the faults inserted in the process with the fault generation module.
Practical possibilities to be done with the optional software Automation Systems Simulation Software (AE-AS):
- Introduction to the SCADA control system.
- OPC server system with Ethernet.
- SCADA control of an automatic industrial system through PC.
UNITÉS SIMILAIRES DISPONIBLES
6.2.6.- SYSTÈMES DE FABRICATION MODULAIRE AVEC PLC
AE-PLC-FMS2
The Flexible Manufacturing System for Transport, Assembly, Selection, Screwing, and Storage, "AE-PLC-FMS2", is a highly adaptable and configurable system designed for the study and application of advanced automation principles within the context...
6.2.6.- SYSTÈMES DE FABRICATION MODULAIRE AVEC PLC
AE-PLC-FMS4
Système de Fabrication Flexible de Filtration, Mélange, Contrôle des Processus Industriels et Embouteillage
The Flexible Manufacturing System for Filtering, Mixing, Industrial Process Control, and Bottling, "AE-PLC-FMS4", is a highly adaptable and configurable system designed for the study and application of advanced automation principles within the...
6.2.6.- SYSTÈMES DE FABRICATION MODULAIRE AVEC PLC
AE-PLC-FMS5
Système de Fabrication Flexible de Transport, Classification, Sélection et Manipulation Pneumatique
Flexible Manufacturing System for Transport, Classification, Selection, and Pneumatic Handling, "AE-PLC-FMS5," is a highly adaptable and configurable system designed for the study and application of advanced automation principles within the...
6.2.6.- SYSTÈMES DE FABRICATION MODULAIRE AVEC PLC
AE-PLC-FMS6
Système de Fabrication Flexible d'Alimentation et de Classification
The Flexible Manufacturing System for Feeding and Classification, "AE-PLC-FMS6", is a highly adaptable and configurable system designed for the study and application of advanced automation principles within the context of Industry 4.0 and Industry...
6.2.6.- SYSTÈMES DE FABRICATION MODULAIRE AVEC PLC
AE-PLC-FMS7
Système de Fabrication Flexible d'Alimentation, Identification, Classification et Transport
The Flexible Manufacturing System for Feeding, Identification, Classification, and Transport, "AE-PLC-FMS7", is a highly adaptable and configurable system designed for the study and application of advanced automation principles within the context...
6.2.6.- SYSTÈMES DE FABRICATION MODULAIRE AVEC PLC
AE-PLC-FMS1
Système de Fabrication Flexible de Transport, Assemblage, Pressage, Sélection, Vissage et Stockage
The Flexible Manufacturing System for Transport, Assembly, Pressing, Selection, Screwing, and Storage, "AE-PLC-FMS1", is a highly adaptable and configurable system designed for the study and application of advanced automation principles within the...
6.2.6.- SYSTÈMES DE FABRICATION MODULAIRE AVEC PLC
AE-PLC-FMS14
Système de Fabrication Flexible de Contrôle des Processus Industriels, Remplissage, Scellage et Stockage
The Flexible Manufacturing System for Industrial Process Control, Filling, Sealing, and Storage, "AE-PLC-FMS14", is a highly adaptable and configurable system designed for the study and application of advanced automation principles within the...
6.2.6.- SYSTÈMES DE FABRICATION MODULAIRE AVEC PLC
AE-PLC-FMS15
Système de Fabrication Flexible d'Alimentation, Assemblage, Manipulation Robotique et Transport
The Flexible Manufacturing System for Feeding, Assembly, Robotic Handling, and Transport, "AE-PLC-FMS15", is a highly adaptable and configurable system designed for the study and application of advanced automation principles within the context of...
EQUIPEMENT COMPLEMENTAIRE
6.2.6.- SYSTÈMES DE FABRICATION MODULAIRE AVEC PLC
AE-PLC-FMS1
Système de Fabrication Flexible de Transport, Assemblage, Pressage, Sélection, Vissage et Stockage
The Flexible Manufacturing System for Transport, Assembly, Pressing, Selection, Screwing, and Storage, "AE-PLC-FMS1", is a highly adaptable and configurable system designed for the study and application of advanced automation principles within the...
6.2.6.- SYSTÈMES DE FABRICATION MODULAIRE AVEC PLC
AE-PLC-FMS2
Système de Fabrication Flexible de Transport, Assemblage, Sélection, Vissage et Stockage
The Flexible Manufacturing System for Transport, Assembly, Selection, Screwing, and Storage, "AE-PLC-FMS2", is a highly adaptable and configurable system designed for the study and application of advanced automation principles within the context...
6.2.6.- SYSTÈMES DE FABRICATION MODULAIRE AVEC PLC
AE-PLC-FMS4
Système de Fabrication Flexible de Filtration, Mélange, Contrôle des Processus Industriels et Embouteillage
The Flexible Manufacturing System for Filtering, Mixing, Industrial Process Control, and Bottling, "AE-PLC-FMS4", is a highly adaptable and configurable system designed for the study and application of advanced automation principles within the...
6.2.6.- SYSTÈMES DE FABRICATION MODULAIRE AVEC PLC
AE-PLC-FMS5
Système de Fabrication Flexible de Transport, Classification, Sélection et Manipulation Pneumatique
Flexible Manufacturing System for Transport, Classification, Selection, and Pneumatic Handling, "AE-PLC-FMS5," is a highly adaptable and configurable system designed for the study and application of advanced automation principles within the...
6.2.6.- SYSTÈMES DE FABRICATION MODULAIRE AVEC PLC
AE-PLC-FMS6
Système de Fabrication Flexible d'Alimentation et de Classification
The Flexible Manufacturing System for Feeding and Classification, "AE-PLC-FMS6", is a highly adaptable and configurable system designed for the study and application of advanced automation principles within the context of Industry 4.0 and Industry...
6.2.6.- SYSTÈMES DE FABRICATION MODULAIRE AVEC PLC
AE-PLC-FMS7
Système de Fabrication Flexible d'Alimentation, Identification, Classification et Transport
The Flexible Manufacturing System for Feeding, Identification, Classification, and Transport, "AE-PLC-FMS7", is a highly adaptable and configurable system designed for the study and application of advanced automation principles within the context...
6.2.6.- SYSTÈMES DE FABRICATION MODULAIRE AVEC PLC
AE-PLC-FMS14
Système de Fabrication Flexible de Contrôle des Processus Industriels, Remplissage, Scellage et Stockage
The Flexible Manufacturing System for Industrial Process Control, Filling, Sealing, and Storage, "AE-PLC-FMS14", is a highly adaptable and configurable system designed for the study and application of advanced automation principles within the...
6.2.6.- SYSTÈMES DE FABRICATION MODULAIRE AVEC PLC
AE-PLC-FMS15
Système de Fabrication Flexible d'Alimentation, Assemblage, Manipulation Robotique et Transport
The Flexible Manufacturing System for Feeding, Assembly, Robotic Handling, and Transport, "AE-PLC-FMS15", is a highly adaptable and configurable system designed for the study and application of advanced automation principles within the context of...
Qualité
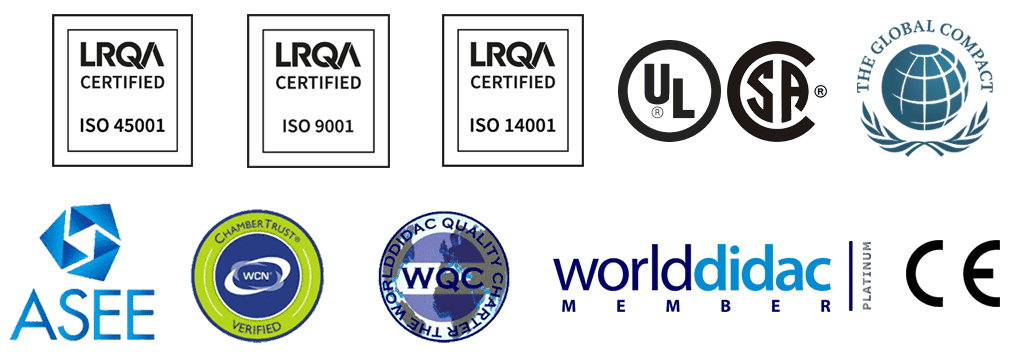
Service après vente
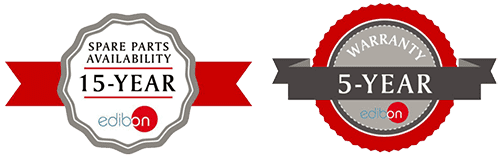