CPIC Station de Contrôle de Processus Industrielles, Contrôlée par Ordinateur (PC)
SYSTEMES INNOVANTS
The Computer Controlled Process Control Plant with Industrial Instrumentation and Service Module (Flow, Temperature, Level and Pressure), "CPIC", is a unit, that offers, on a reasonable laboratory scale, the different process and elements that are commonly used by any kind the industry.
Expansions
Laboratories
NOUVELLES LIÉES
Description Générale
The Computer Controlled Process Control Plant with Industrial Instrumentation and Service Module (Flow, Temperature, Level and Pressure),"CPIC", is a unit, that offers, on a reasonable laboratory scale, the different process and elements that are commonly used by any kind theindustry. It also shows the complexity that can take place while controlling in processes the same variable.
"CPIC" is made up of a main unit where the different elements are installed and a service module that provides cold and hot water, as wellas compressed air, necessary for the unit to work.
This Computer Controlled Unit is supplied with the EDIBON Computer Control System (SCADA), and includes: The unit itself + aControl Interface Box + a Data Acquisition Board + Computer Control, Data Acquisition and Data Management Software Packages, forcontrolling the process and all parameters involved in the process.
Accessoires
Station de Contrôle de Processus Industrielles (seulement Température),Contrôlée par Ordinateur (PC)
Station de Contrôle de Processus Industrielles (seulement Niveau), Contrôlée par Ordinateur (PC)
Station de Contrôle de Processus Industrielles (seulement Pression), Contrôlée par Ordinateur (PC)
Des exercices et pratiques guidées
EXERCICES GUIDÉS INCLUS DANS LE MANUEL
- Familiarization with the different components of the system and their symbolic representation. Identification of components and description of their functions.
- The auxiliary systems: air and hot water supply.
- Flow sensors calibration.
- Temperature sensors calibration.
- Level sensor calibration.
- I/P converter calibration.
- Flow control loop (on/off).
- Flow control loop (proportional).
- Flow control loop (P+I).
- Flow control loop (P+D).
- Flow control loop (P+I+D).
- Adjust of the flow controller constants (Ziegler-Nichols).
- Adjust of the flow controller constants (reaction curves).
- Search of simple shortcomings in the loop of flow control.
- Temperature control loop (on/off).
- Temperature control loop (proportional).
- Temperature control loop (P+I).
- Temperature control loop (P+D).
- Temperature control loop (P+I+D).
- Adjust of the temperature controller constants (minimum area or reduction rate).
- Adjust of the temperature controller constants (minimum disturbance criterion).
- Adjust of the temperature controller constants (minimum width criterion).
- Study of the retards for speed/distance, exemplified through the temperature control loop.
- Study of the energy lost in the temperature control loop.
- Search of simple shortcomings in temperature control loop.
- Level control loop (on/off).
- Level control loop (proportional).
- Level control loop (P+I).
- Level control loop (P+D).
- Level control loop (P+I+D).
- Adjust of the level controller constants (minimum area or reduction rate).
- Adjust of the level controller constants (minimum disturbance criterion).
- Adjust of the level controller constants (minimum width criterion).
- Search of simple shortcomings in level control loop.
- Pressure control loop (on/off).
- Pressure control loop (proportional).
- Pressure control loop (P+I).
- Pressure control loop (P+D).
- Pressure control loop (P+I+D).
- Adjust of the pressure controller constants (minimum area or reduction rate).
- Adjust of the pressure controller constants (minimum disturbancecriterion).
- Adjust of the pressure controller constants (minimum width criterion).
- Search of simple shortcomings in the pressure control loop.
- The use of the controllers in cascade, exemplified with the level/flow control loop.
- Adjust of cascade control constants (minimum area or reduction rate).
- Adjust of cascade control constants (minimum disturbance criterion).
- Adjust of cascade control constants (minimum width criterion).
- Search of simple shortcomings in cascade control loop.
- Practical operation of the control plant to some wanted specific values: transfers without interferences.
- Calculation of the fluid flow in function of the differential pressure sensor.
PLUS D'EXERCICES PRATIQUES À EFFECTUER AVEC CETTE ÉQUIPEMENT
- Many students view results simultaneously. To view all results in real time in the classroom by means of a projector or an electronic whiteboard.
- Open Control, Multicontrol and Real Time Control. This unit allows intrinsically and/or extrinsically to change the span, gains, proportional, integral, derivative parameters, etc, in real time.
- The Computer Control System with SCADA and PID Control allow a real industrial simulation.
- This unit is totally safe as uses mechanical, electrical and electronic, and software safety devices.
- This unit can be used for doing applied research.
- This unit can be used for giving training courses to Industries even to other Technical Education Institutions.
- Control of the CPIC unit process through the control interface box without the computer.
- Visualization of all the sensors values used in the CPIC unit process.
- By using PLC-PI additional 19 more exercises can be done.
- Several other exercises can be done and designed by the user.
EQUIPEMENT COMPLEMENTAIRE
Système de Réservoirs Couplés, Contrôlé par Ordinateur (PC)
Unité de Contrôle de Processus (Valve Électronique), Contrôlee par Ordinateur (PC)
Unité de Contrôle de Processus (Valve Pneumatique), Contrôlée par Ordinateur (PC)
Unité de Contrôle de Processus (Variateur de la vitesse), Contrôlée par Ordinateur (PC)
Contrôle de Processus (Valve Électronique + Pneumatique et Variateur), Contrôlée par Ordinateur (PC)
Unité de Contrôle de Processus pour l´Étude de la Pression (Air), Contrôlée par Ordinateur (PC)
Station de Contrôle de Processus Industrielles (seulement Débit), Contrôlée par Ordinateur (PC)
Station de Contrôle de Processus Industrielles (seulement Température),Contrôlée par Ordinateur (PC)
Station de Contrôle de Processus Industrielles (seulement Niveau), Contrôlée par Ordinateur (PC)
Station de Contrôle de Processus Industrielles (seulement Pression), Contrôlée par Ordinateur (PC)
Qualité
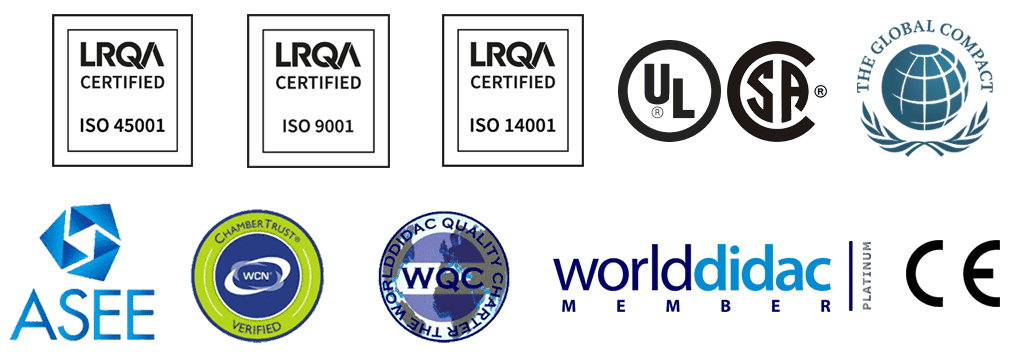
Service après vente
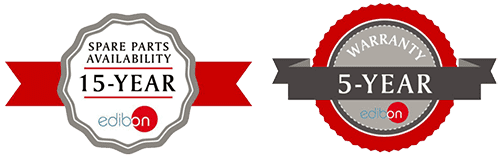