TIPL Plate Heat Exchanger for TICC
INNOVATIVE SYSTEMS
The Plate Heat Exchanger for TICC, "TIPL", designed by EDIBON, allows the study of heat transfer between hot and cold water flowing through alternate channels formed between parallel plates. This unit enables the analysis of how heat transfer varies under different conditions, such as changes in flow rate, temperature, and flow type (counter-current or parallel).
Expansions
Laboratories
RELATED NEWS
General Description
The Plate Heat Exchanger for TICC, "TIPL", designed by EDIBON, allows the study of heat transfer between hot and cold water flowing through alternate channels formed between parallel plates. This unit enables the analysis of how heat transfer varies under different conditions, such as changes in flow rate, temperature, and flow type (counter-current or parallel).
With a plate arrangement that optimizes heat transfer, the Plate Heat Exchanger for TICC offers an effective tool for heat exchange analysis and experimentation.
The plate heat exchanger allows detailed study and analysis of heat transfer between two fluids flowing through alternate channels formed between parallel plates. This includes investigating the efficiency of the exchanger, studying the effectiveness of heat exchange, assessing the influence of flow rate on heat transfer, and comparing different flow configurations, such as counter-current and parallel flow. Additionally, this unit allows specific practices to be developed for determining the overall energy balance in the exchanger, calculating exchanger effectiveness using the NTU method, and studying the influence of Reynolds number on heat transfer.
The plate heat exchanger enables temperature measurement at various points within the exchanger, providing a detailed understanding of thermal distribution within the unit.
In summary, the Plate Heat Exchanger for TICC, "TIPL", offers students, professors, and researchers the opportunity to thoroughly understand and practice the fundamental principles of heat transfer and its application in industry, thanks to its parallel plate design.
To work with this unit, the Base and Service Unit, "TIUS", is required, which provides key functions such as heating water using a thermostatic bath, pumping hot water, regulating and measuring the flow rates of cold and hot water, measuring the inlet and outlet temperatures of cold and hot water, as well as measuring the pressure drop in the heat exchanger.
These Computer Controlled Units are supplied with EDIBON Computer Control System (SCADA), and includes: The unit itself + a Control Interface Box + a Data Acquisition Board + Computer Control, Data Acquisition and Data Management Software Packages, for controlling the process and all parameters involved in the process.
Exercises and guided practices
GUIDED PRACTICAL EXERCISES INCLUDED IN THE MANUAL
- Global energy balance in the heat exchanger and the study of losses.
- Exchanger effectiveness determination. NTU Method.
- Study of the heat transfer under counter-current and co-current flow conditions.
- Flow influence on the heat transfer. Reynolds number calculation.
- Sensors calibration.
MORE PRACTICAL EXERCISES TO BE DONE WITH THE UNIT
- Study of the hysteresis of the flow sensor.
Other possibilities to be done with this unit:
- Many students view results simultaneously. To view all results in real time in the classroom by means of a projector or an electronic whiteboard.
- Open Control, Multicontrol and Real Time Control. This unit allows intrinsically and/or extrinsically to change the span, gains, proportional, integral, derivative parameters, etc, in real time.
- The Computer Control System with SCADA and PID Control allow a real industrial simulation.
- This unit is totally safe as uses mechanical, electrical and electronic, and software safety devices.
- This unit can be used for doing applied research.
- This unit can be used for giving training courses to Industries even to other Technical Education Institutions.
- Control of the TICC unit process through the control interface box without the computer.
- Visualization of all the sensors values used in the TICC unit process.
- By using PLC-PI additional 19 more exercises can be done.
- Several other exercises can be done and designed by the user.
SIMILAR UNITS AVAILABLE
Shell & Tube Heat Exchanger for TICC
Concentric Tube Heat Exchanger for TICC
Jacketed Vessel Heat Exchanger for TICC
Coil Vessel Heat Exchanger for TICC
Extended Concentric Tube Heat Exchanger for TICC
Extended Plate Heat Exchanger for TICC
Cross Flow Heat Exchanger for TICC
SUPPLEMENTARY EQUIPMENT
Computer Controlled Heat Exchangers Training System
Base Service Unit (Common for all available Heat Exchangers type "TI")
Concentric Tube Heat Exchanger for TICC
Extended Concentric Tube Heat Exchanger for TICC
Extended Plate Heat Exchanger for TICC
Shell & Tube Heat Exchanger for TICC
Jacketed Vessel Heat Exchanger for TICC
Coil Vessel Heat Exchanger for TICC
Turbulent Flow Heat Exchanger for TICC
Cross Flow Heat Exchanger for TICC
Heat exchanger Training System
Base Service Unit (Common for all available Heat Exchangers type "TI..B")
Quality
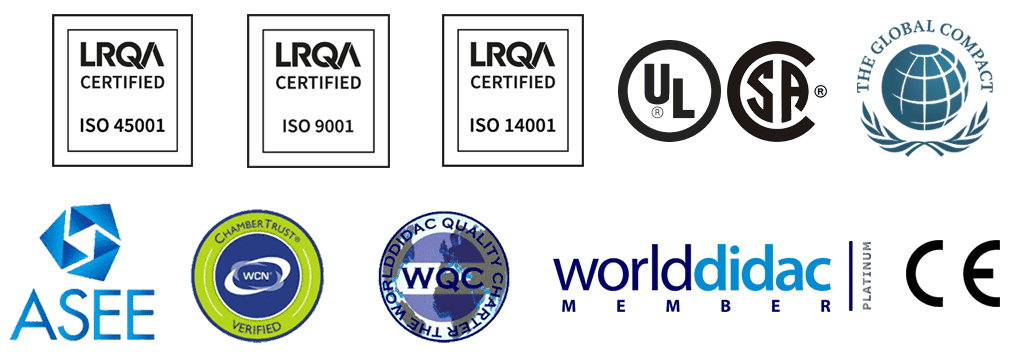
AFTER-SALES SERVICE
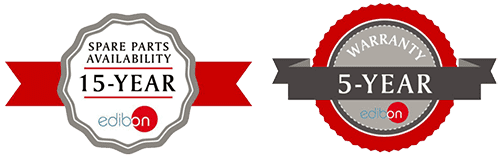