TIAAC Computer Controlled Water-to-Air Heat Exchanger Unit
INNOVATIVE SYSTEMS
The Computer Controlled Water-to-Air Heat Exchanger Unit, "TIAAC", includes a stainless steel duct with a heat exchanger in its center and a centrifugal fan at one end. The fan impels the air through the heat exchanger.
Expansions
Laboratories
RELATED NEWS
General Description
The Computer Controlled Water-to-Air Heat Exchanger Unit, "TIAAC", includes a stainless steel duct with a heat exchanger in its center and a centrifugal fan at one end. The fan impels the air through the heat exchanger.
The heat exchanger consists of a finned radiator through which a hot water flow coming from a tank circulates. This radiator is placed perpendicular to an air flow generated by the fan (computer controlled).
Hot water flows through a closed circuit. A heating element (computer controlled) immersed in the stainless steel tank heats water to a specific temperature. Water leaves the tank and is impelled by a pump (computer controlled). Part of the water enters the exchanger and part returns to the tank by a bypass. The bypass has a valve to regulate the flow of hot water. Water passes through a flow sensor at the exchanger’s inlet.
The hot water circuit has two ball valves to control and drain hot water at the exchanger.
There is a series of temperature sensors that allow to measure the temperature at the inlet and outlet of the exchanger of both the hot water and air, and the water temperature in the tank. There is a water flow sensor and an air flow sensor to measure the hot and cold flow.
The tank includes a level switch to guarantee a specific level inside the tank and there is a pressure sensor after the pump that allows to study the characteristic curve of the pump.
This Computer Controlled Unit is supplied with the EDIBON Computer Control System (SCADA), and includes: The unit itself + a Control Interface Box + a Data Acquisition Board + Computer Control, Data Acquisition and Data Management Software Packages, for controlling the process and all parameters involved in the process.
Exercises and guided practices
GUIDED PRACTICAL EXERCISES INCLUDED IN THE MANUAL
- Familiarization with water to air heat exchangers.
- Study of the overall energy balance in the heat exchanger and study of losses.
- Determination of the heat exchanger efficiency. NTU method.
- Study of the influence of flow in the heat transfer. Calculation of Reynolds number.
- Study of the characteristic curve of the pump.
- Sensors calibration.
MORE PRACTICAL EXERCISES TO BE DONE WITH THE UNIT
Additional practical possibilities:
- Study of the effect of the temperature gradient on the heat transfer coefficient.
- Determination of water and air thermal flows.
Other possibilities to be done with this Unit:
- Many students view results simultaneously. To view all results in real time in the classroom by means of a projector or an electronic whiteboard.
- Open Control, Multicontrol and Real Time Control. This unit allows intrinsically and/or extrinsically to change the span, gains, proportional, integral, derivative parameters, etc, in real time.
- The Computer Control System with SCADA and PID Control allow a real industrial simulation.
- This unit is totally safe as uses mechanical, electrical and electronic, and software safety devices.
- This unit can be used for doing applied research.
- This unit can be used for giving training courses to Industries even to other Technical Education Institutions.
- Control of the TIAAC unit process through the control interface box without the computer.
- Visualization of all the sensors values used in the TIAAC unit process.
- By using PLC-PI additional 19 more exercises can be done.
- Several other exercises can be done and designed by the user.
SIMILAR UNITS AVAILABLE
SUPPLEMENTARY EQUIPMENT
Computer Controlled Heat Exchangers Training System
Base Service Unit (Common for all available Heat Exchangers type "TI")
Concentric Tube Heat Exchanger for TICC
Extended Concentric Tube Heat Exchanger for TICC
Plate Heat Exchanger for TICC
Extended Plate Heat Exchanger for TICC
Shell & Tube Heat Exchanger for TICC
Jacketed Vessel Heat Exchanger for TICC
Coil Vessel Heat Exchanger for TICC
Turbulent Flow Heat Exchanger for TICC
Cross Flow Heat Exchanger for TICC
Heat exchanger Training System
Quality
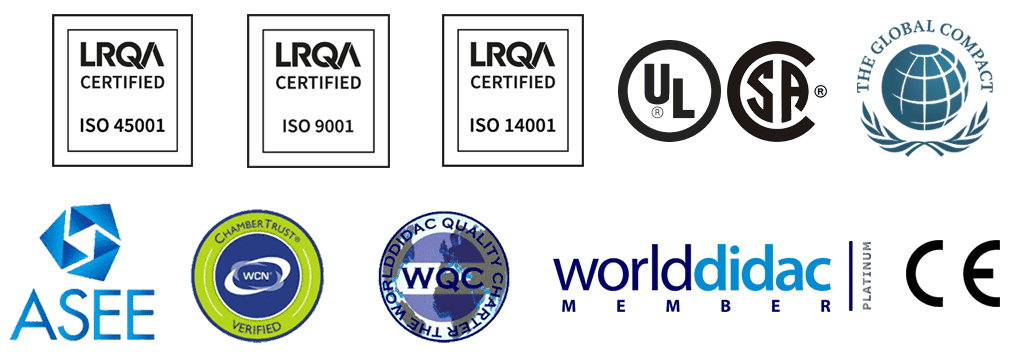
AFTER-SALES SERVICE
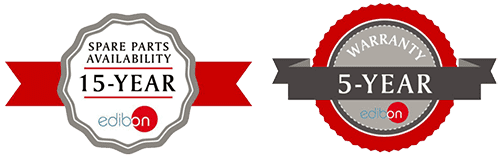