TFLVC Computer Controlled Laminar/Viscous Flow Heat Transfer Unit
INNOVATIVE SYSTEMS
The Computer Controlled Laminar/Viscous Flow Heat Transfer Unit, "TFLVC", is a laboratory scale unit designed to study heat transfer between hot oil flowing in laminar flow through an internal tube and cold water that flows through the annulus (ring-shaped area).
Expansions
Laboratories
RELATED NEWS
General Description
The Computer Controlled Laminar/Viscous Flow Heat Transfer Unit, "TFLVC", is a laboratory scale unit designed to study heat transfer between hot oil flowing in laminar flow through an internal tube and cold water that flows through the annulus (ring-shaped area).
Oil circuit (hot fluid):
- The hot oil flows along a closed circuit through the internal tube of the exchanger. An electric heating element, placed in the heating tank, heats the oil up to a specific temperature. This temperature is controlled by the heating element (PID control), limiting the temperature to 90 ºC. The oil goes out of the tank impelled by a pump. A flow sensor measures the oil flow. The oil cools down along the exchanger and then returns to the heating tank, starting a new cycle. There is a regulation valve at the inlet of the heating tank to determine the flow rate of hot oil in the circuit.
- The flow of oil can also be controlled by changing the speed of the pump through the software and with the regulation valve located in the bypass.
- There is a purge valve in the circuit to drain and clean the circuit and the heating tank.
Water circuit (cold fluid):
- The cold water comes from of the tap and flows through the annulus formed between the internal and external tube of the exchanger.
- The cold water flow is controlled by a regulation valve and is measured by a flow sensor. Water enters the exchanger and its temperature rises. Afterwards, water goes out of the system.
- The cold water can enter the exchanger by both ends (co-current or counter-current flow), depending of the position of the valves.
This Computer Controlled Unit is supplied with the EDIBON Computer Control System (SCADA), and includes: The unit itself + a Control Interface Box + a Data Acquisition Board + Computer Control, Data Acquisition and Data Management Software Packages, for controlling the process and all parameters involved in the process.
Exercises and guided practices
GUIDED PRACTICAL EXERCISES INCLUDED IN THE MANUAL
- Demonstration of a concentric tube heat exchanger with cocurrent and counter-current flow in laminar/viscous flow.
- Energy balance of the heat exchanger.
- Determination of surface heat transfer coefficients on the oil and water sides and determination of the overall heat transfer coefficient.
- Flow influence on the heat transfer. Reynolds number calculation.
- Relationship between Nusselt Number and Graetz Number for Reynolds Numbers up to 1400.
- Sensors calibration.
MORE PRACTICAL EXERCISES TO BE DONE WITH THE UNIT
- Many students view results simultaneously. To view all results in real time in the classroom by means of a projector or an electronic whiteboard.
- Open Control, Multicontrol and Real Time Control. This unit allows intrinsically and/or extrinsically to change the span, gains, proportional, integral, derivative parameters, etc, in real time.
- The Computer Control System with SCADA and PID Control allow a real industrial simulation.
- This unit is totally safe as uses mechanical, electrical and electronic, and software safety devices.
- This unit can be used for doing applied research.
- This unit can be used for giving training courses to Industries even to other Technical Education Institutions.
- Control of the TFLVC unit process through the control interface box without the computer.
- Visualization of all the sensors values used in the TFLVC unit process.
- By using PLC-PI additional 19 more exercises can be done.
- Several other exercises can be done and designed by the user.
SIMILAR UNITS AVAILABLE
SUPPLEMENTARY EQUIPMENT
Computer Controlled Heat Exchangers Training System
Base Service Unit (Common for all available Heat Exchangers type "TI")
Concentric Tube Heat Exchanger for TICC
Extended Concentric Tube Heat Exchanger for TICC
Plate Heat Exchanger for TICC
Extended Plate Heat Exchanger for TICC
Shell & Tube Heat Exchanger for TICC
Jacketed Vessel Heat Exchanger for TICC
Coil Vessel Heat Exchanger for TICC
Turbulent Flow Heat Exchanger for TICC
Cross Flow Heat Exchanger for TICC
Heat exchanger Training System
Quality
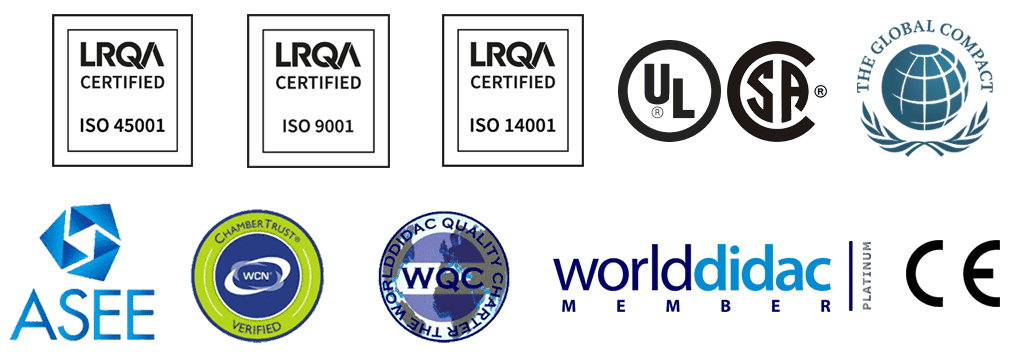
AFTER-SALES SERVICE
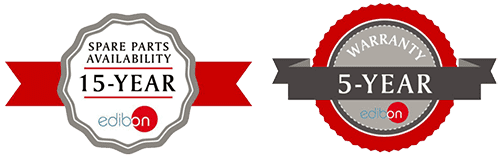