EBDC Computer Controlled Biodiesel Process Unit
INNOVATIVE SYSTEMS
The Computer Controlled Biodiesel Process Unit, "EBDC", allows the production of biodiesel from vegetable oil by studying the main parameters that influence the performance of the process and the final quality of the product. Among these parameters are the operating temperature, the amount of catalyst used and the operating time.
Expansions
Laboratories
RELATED NEWS
General Description
The process carried out by the Computer Controlled Biodiesel Process Unit, "EBDC", consists of the transformation of the fatty acids from vegetable oils into a biofuel of high energetic power.
The process basically consists of two well-defined stages:
- Stage I: Mixing and reaction under agitation. This first stage begins with the addition of vegetable oil to the main tank (reactor), and the preparation of the catalyst in a smaller secondary reactor. Next, reagent and catalyst are combined by subjecting the mixture to intense agitation and homogeneous heating, this is achieved by recirculating the medium through a centrifugal pump and providing heat by means of an electrical resistance, both actuators are computer controlled. This stage is carried out in a stainless steel reactor with temperature sensor and level switches that allow a controlled and safe operation.
- Stage II: Separation and washing of the obtained products. A second fundamental stage after the reaction is the separation of the main product from the rest of the by-products found in the medium. This is done by means of a first biphasic decantation. Decanting is a suitable operation when the compounds to be separated are not miscible with each other, which is the case between biodiesel and glycerin. Glycerin has a higher density than the fuel, so it is easily removed through the conical bottom of the reactor. On the other hand, the biodiesel undergoes a washing stage in which it is recirculated through a small ion exchange column that allows the elimination of impurities and water that may remain after the reaction. Finally, the fuel is passed through a diesel filter before final storage.
Additionally, the performance of the unit and the quality of the biodiesel can be evaluated thanks to a load cell installed in the product tank and a titration kit (pipette, drippers, etc.).
This Computer Controlled Unit is supplied with the EDIBON Computer Control System (SCADA), and includes: The unit itself + a Control Interface Box + a Data Acquisition Board + Computer Control, Data Acquisition and Data Management Software Packages, for controlling the process and all parameters involved in the process.
Exercises and guided practices
GUIDED PRACTICAL EXERCISES INCLUDED IN THE MANUAL
- Study and performance of tests to determine the appropriate amount of catalyst to be used in the biodiesel generation process (titration).
- Familiarization with the operation of a biodiesel production unit during the products reaction, extraction and washing process.
- Study of the agitation and mixing level influence on the final quality of the obtained biodiesel.
- Study of the washing and purifying stage influence on the final quality of the obtained biodiesel.
- Study of the influence of temperature during the vegetable oils preheating and reaction stage on the final quality of the obtained biodiesel.
- Analysis and tests to determine the biodiesel quality.
MORE PRACTICAL EXERCISES TO BE DONE WITH THE UNIT
- Study of vegetable oils transesterification with an alcohol to produce biodiesel.
- Sensors calibration.
Other possibilities to be done with this Unit:
- Many students view results simultaneously. To view all results in real time in the classroom by means of a projector or an electronic whiteboard.
- Open Control, Multicontrol and Real Time Control. This unit allows intrinsically and/or extrinsically to change the span, gains, proportional, integral, derivative parameters, etc, in real time.
- The Computer Control System with SCADA and PID Control allow a real industrial simulation.
- This unit is totally safe as uses mechanical, electrical and electronic, and software safety devices.
- This unit can be used for doing applied research.
- This unit can be used for giving training courses to Industries even to other Technical Education Institutions.
- Control of the EBDC unit process through the control interface box without the computer.
- Visualization of all the sensors values used in the EBDC unit process.
- By using PLC-PI additional 19 more exercises can be done.
- Several other exercises can be done and designed by the user.
SIMILAR UNITS AVAILABLE
SUPPLEMENTARY EQUIPMENT
Computer Controlled and Touch Screen 60 l Semicontinuous Centrifugal Separator
Computer Controlled and Touch Screen 1000 l Semicontinuous Centrifugal Separator
Computer Controlled Bioethanol Process Unit
Bioethanol Process Unit
Computer Controlled and Touch Screen Biogas Processing Plant
Computer Controlled Biogas Process Unit
Biogas Process Unit
Biodiesel Process Unit
Computer Controlled Biomass Process Unit
Biomass Process Unit
Quality
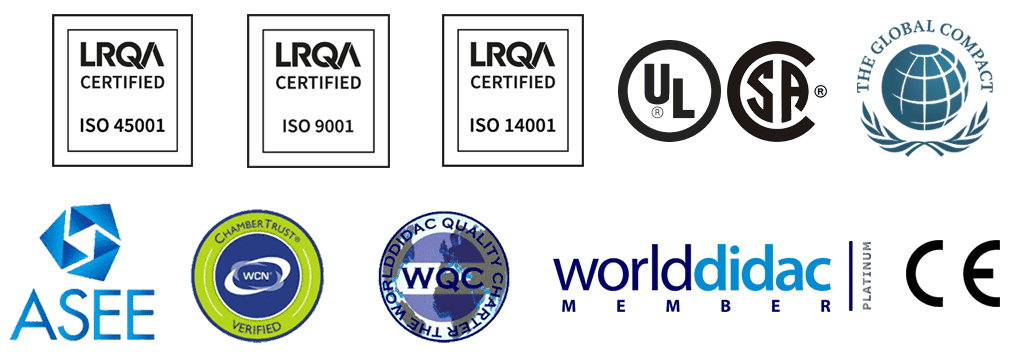
AFTER-SALES SERVICE
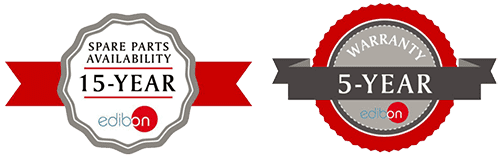