At EDIBON, we are committed to strengthening skills as a strategic pillar for the competitiveness and social well-being of the European Union. Proper training not only boosts the economy but also enables individuals to fully participate in society and democracy.
AE-PLC-FMS4 Flexible Manufacturing System for Filtering, Mixing, Industrial Process Control, and Bottling
INNOVATIVE SYSTEMS
The Flexible Manufacturing System for Filtering, Mixing, Industrial Process Control, and Bottling, "AE-PLC-FMS4", designed by EDIBON, enables the study and practice of an automated production cycle consisting of 4 distinct workstations. This system integrates all the mentioned workstations, as well as an additional feeding station.
RELATED NEWS
General Description
The Flexible Manufacturing System for Filtering, Mixing, Industrial Process Control, and Bottling, "AE-PLC-FMS4", is a highly adaptable and configurable system designed for the study and application of advanced automation principles within the context of Industry 4.0 and Industry 5.0. This unit integrates key technologies such as automated control, inter-device networking through smart networks, PLC programming of assembly lines, and real-time data analysis, allowing users to explore the capabilities of digitized and connected manufacturing that characterize the Fourth Industrial Revolution and pave the way for the Fifth Industrial Revolution.
It consists of four interconnected stations that perform specific tasks related to feeding, transport, assembly, sorting (dimension, material, and color), screwing, and parts storage. Each of these workstations requires its own PLC from the selected brand (PANASONIC, SIEMENS, ALLEN BRADLEY, MITSUBISHI and/or OMRON), allowing users to explore how advanced control and production concepts are applied in an automated manufacturing line. The workflow is coordinated by a central PLC system (from the same brand chosen for the stations) and an Ethernet network, making the "AE-PLC-FMS4" a comprehensive learning resource for those interested in automation engineering and flexible manufacturing.
The included workstations are:
- Filtration Workstation, "AE-PLC-FT": Performs the initial filtration of incoming water, ensuring it is free of impurities. Once filtered, the water is pumped to the next station.
- Mixing Workstation, "AE-PLC-MS": At this stage, the water is properly mixed and then pumped to the Industrial Process Control station to continue the production process.
- Process Control Workstation, "AE-PLC-CP": Here, three different industrial controllers monitor and regulate critical product parameters, such as temperature, level, flow rate, and pressure, ensuring quality and consistency throughout the process.
- Bottling Workstation, "AE-PLC-MEMB": Finally, this station is responsible for bottling the product, completing the flexible manufacturing process.
The system allows students and instructors to delve into fundamental concepts of industrial automation. Through its use, students acquire practical skills in designing and operating automated systems, gaining a deep understanding of the coordinated work across the various workstations of a real production line. This configurable system has been carefully designed so that each of its workstations performs specific functions that simulate real industrial processes.
The recommended Automation System Simulation Software, "AE-AS," enables the simulation of industrial processes in both 2D and 3D, providing full control and supervision, allowing users to safely experiment with automation software in a protected environment.
Exercises and guided practices
GUIDED PRACTICAL EXERCISES INCLUDED IN THE MANUAL
Practical possibilities to be done with the Flexible Manufacturing System for Filtering, Mixing, Industrial Process Control, and Bottling (AE-PLC-FMS4):
- Introduction to flexible manufacturing system (FMS).
- Introduction to pneumatics and electro-pneumatics.
- Introduction to vacuum technology.
- Study of the sensor detection.
- Testing the digital inputs and outputs of the automatic system through a PLC.
- Modify manufacturing parameters through the PLC.
- Configuration of a pneumatic application.
- Introduction to the Human-machine interface systems (HMI).
- Study of an automatic control of an industrial system.
- Control of the flexible manufacturing system through a central PLC in an Ethernet network with local PLC in each workstation.
- Manage the flexible manufacturing system through the HMI device.
Practical possibilities to be done with the workstation alone:- Filtration Workstation (AE-PLC-FT).
- Manual control of a Filtration system.
- Automatic control of a Filtration system.
- Change the parameters of the Filtration process.
- Optimize the process time.
- Study and analysis of the faults inserted in the process with the fault generation module.
- Mixing Workstation (AE-PLC-MS).
- Manual control of a mixing system.
- Automatic control of a mixing system.
- Change the parameters of the mixing process.
- Optimization of the process time.
- Study and analysis of the faults inserted in the process with the fault generation module.
- Process Control Workstation (AE-PLC-CP).
- Manual control of a water tank temperature.
- Manual control of a water tank level.
- Manual control of a water flow.
- Manual control of a water pressure.
- Automatic control of a water tank temperature through an industrial controller.
- Automatic control of a water tank level through an industrial controller.
- Automatic control of a water flow through an industrial controller.
- Automatic control of a water pressure through an industrial controller.
- Change the parameters of the different controls.
- Optimize the process time of the different industrial controls.
- Study and analysis of the faults inserted in the process with the fault generation module.
- Bottling Workstation (AE-PLC-MEMB).
- Manual control of the bottling system.
- Automatic control of the bottling system.
- Change the parameters of the bottling process.
- Optimize the process time.
- Study and analysis of the faults inserted in the process with the fault generation module.
Practical possibilities to be done with the optional software Automation Systems Simulation Software (AE-AS):
- Introduction to the SCADA control system.
- OPC server system with Ethernet.
- SCADA control of an automatic industrial system through PC.
SIMILAR UNITS AVAILABLE
6.2.6.- FLEXIBLE MANUFACTURING SYSTEMS WITH PLC
AE-PLC-FMS2
The Flexible Manufacturing System for Transport, Assembly, Selection, Screwing, and Storage, "AE-PLC-FMS2", is a highly adaptable and configurable system designed for the study and application of advanced automation principles within the context...
6.2.6.- FLEXIBLE MANUFACTURING SYSTEMS WITH PLC
AE-PLC-FMS3
Flexible Manufacturing System for Transport, Assembly, Selection (Material and Color), and Storage
The Flexible Manufacturing System for Transport, Assembly, Selection (Material and Color), and Storage, "AE-PLC-FMS3", is a highly adaptable and configurable system designed for the study and application of advanced automation principles within...
6.2.6.- FLEXIBLE MANUFACTURING SYSTEMS WITH PLC
AE-PLC-FMS5
Flexible Manufacturing System for Transport, Classification, Selection, and Pneumatic Handling
Flexible Manufacturing System for Transport, Classification, Selection, and Pneumatic Handling, "AE-PLC-FMS5," is a highly adaptable and configurable system designed for the study and application of advanced automation principles within the...
6.2.6.- FLEXIBLE MANUFACTURING SYSTEMS WITH PLC
AE-PLC-FMS6
Flexible Manufacturing System for Feeding and Classification
The Flexible Manufacturing System for Feeding and Classification, "AE-PLC-FMS6", is a highly adaptable and configurable system designed for the study and application of advanced automation principles within the context of Industry 4.0 and Industry...
6.2.6.- FLEXIBLE MANUFACTURING SYSTEMS WITH PLC
AE-PLC-FMS7
Flexible Manufacturing System for Feeding, Identification, Classification, and Transport
The Flexible Manufacturing System for Feeding, Identification, Classification, and Transport, "AE-PLC-FMS7", is a highly adaptable and configurable system designed for the study and application of advanced automation principles within the context...
6.2.6.- FLEXIBLE MANUFACTURING SYSTEMS WITH PLC
AE-PLC-FMS1
Flexible Manufacturing System for Transport, Assembly, Pressing, Selection, Screwing, and Storage
The Flexible Manufacturing System for Transport, Assembly, Pressing, Selection, Screwing, and Storage, "AE-PLC-FMS1", is a highly adaptable and configurable system designed for the study and application of advanced automation principles within the...
6.2.6.- FLEXIBLE MANUFACTURING SYSTEMS WITH PLC
AE-PLC-FMS14
Flexible Manufacturing System for Industrial Process Control, Filling, Sealing, and Storage
The Flexible Manufacturing System for Industrial Process Control, Filling, Sealing, and Storage, "AE-PLC-FMS14", is a highly adaptable and configurable system designed for the study and application of advanced automation principles within the...
6.2.6.- FLEXIBLE MANUFACTURING SYSTEMS WITH PLC
AE-PLC-FMS15
Flexible Manufacturing System for Feeding, Assembly, Robotic Handling, and Transport
The Flexible Manufacturing System for Feeding, Assembly, Robotic Handling, and Transport, "AE-PLC-FMS15", is a highly adaptable and configurable system designed for the study and application of advanced automation principles within the context of...
SUPPLEMENTARY EQUIPMENT
6.2.6.- FLEXIBLE MANUFACTURING SYSTEMS WITH PLC
AE-PLC-FMS1
Flexible Manufacturing System for Transport, Assembly, Pressing, Selection, Screwing, and Storage
The Flexible Manufacturing System for Transport, Assembly, Pressing, Selection, Screwing, and Storage, "AE-PLC-FMS1", is a highly adaptable and configurable system designed for the study and application of advanced automation principles within the...
6.2.6.- FLEXIBLE MANUFACTURING SYSTEMS WITH PLC
AE-PLC-FMS2
Flexible Manufacturing System for Transport, Assembly, Selection, Screwing, and Storage
The Flexible Manufacturing System for Transport, Assembly, Selection, Screwing, and Storage, "AE-PLC-FMS2", is a highly adaptable and configurable system designed for the study and application of advanced automation principles within the context...
6.2.6.- FLEXIBLE MANUFACTURING SYSTEMS WITH PLC
AE-PLC-FMS3
Flexible Manufacturing System for Transport, Assembly, Selection (Material and Color), and Storage
The Flexible Manufacturing System for Transport, Assembly, Selection (Material and Color), and Storage, "AE-PLC-FMS3", is a highly adaptable and configurable system designed for the study and application of advanced automation principles within...
6.2.6.- FLEXIBLE MANUFACTURING SYSTEMS WITH PLC
AE-PLC-FMS5
Flexible Manufacturing System for Transport, Classification, Selection, and Pneumatic Handling
Flexible Manufacturing System for Transport, Classification, Selection, and Pneumatic Handling, "AE-PLC-FMS5," is a highly adaptable and configurable system designed for the study and application of advanced automation principles within the...
6.2.6.- FLEXIBLE MANUFACTURING SYSTEMS WITH PLC
AE-PLC-FMS6
Flexible Manufacturing System for Feeding and Classification
The Flexible Manufacturing System for Feeding and Classification, "AE-PLC-FMS6", is a highly adaptable and configurable system designed for the study and application of advanced automation principles within the context of Industry 4.0 and Industry...
6.2.6.- FLEXIBLE MANUFACTURING SYSTEMS WITH PLC
AE-PLC-FMS7
Flexible Manufacturing System for Feeding, Identification, Classification, and Transport
The Flexible Manufacturing System for Feeding, Identification, Classification, and Transport, "AE-PLC-FMS7", is a highly adaptable and configurable system designed for the study and application of advanced automation principles within the context...
6.2.6.- FLEXIBLE MANUFACTURING SYSTEMS WITH PLC
AE-PLC-FMS14
Flexible Manufacturing System for Industrial Process Control, Filling, Sealing, and Storage
The Flexible Manufacturing System for Industrial Process Control, Filling, Sealing, and Storage, "AE-PLC-FMS14", is a highly adaptable and configurable system designed for the study and application of advanced automation principles within the...
6.2.6.- FLEXIBLE MANUFACTURING SYSTEMS WITH PLC
AE-PLC-FMS15
Flexible Manufacturing System for Feeding, Assembly, Robotic Handling, and Transport
The Flexible Manufacturing System for Feeding, Assembly, Robotic Handling, and Transport, "AE-PLC-FMS15", is a highly adaptable and configurable system designed for the study and application of advanced automation principles within the context of...
Quality
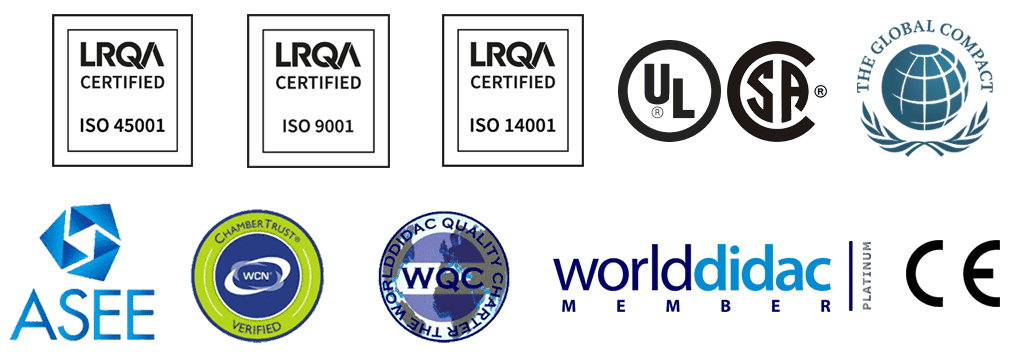
AFTER-SALES SERVICE
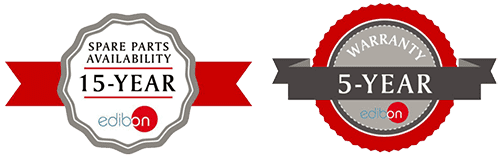