HCDEC Gerät für Versuche mit einem Zwei-Stufen-Kompressor, computergesteuert (PC)
INNOVATIVE SYSTEME
The Computer Controlled Two-Stage Compressor Test Unit, "HCDEC", is a unit that allows for studying single-stage compression and two-stage compression (compression work, efficiency, P-V curves and thermodynamic properties among others). Besides, it allows for studying compression with and without refrigeration in the intermediate stage.
Erweiterungen
Laboratorien
ÄHNLICHE NEUIGKEITEN
ALLGEMEINE BESCHREIBUNG
The Computer Controlled Two-Stage Compressor Test Unit, "HCDEC", works with compressed air and presents as a principal device a compression bench with two pistons, low and high pressure.
This unit presents four circuits or work dispositions which allow to study the different compression situations.
In the four selectable circuits that the unit presents, it can be identified the similar first stage where the air enters by aspiration of the compressor piston. In this first stage the air pass through a priming vessel where the condensates are collected, the air pass across the flow sensor, temperature sensor and pressure sensor which collect the information through the computer. The first stage presents a pressure gauge and air filter too.
After this first stage, the unit presents different compression situations which offer the data of each compression points through three different temperature and pressure sensors. The unit presents a concentric tubes heat exchanger which cools down the compressed air stream with refrigeration water, two temperature sensors collect the data and allow to do the heat balance calculation in the device, and study the influence of this device over this type of process.
The unit allows for studying different compression situations:
a) Compression in one stage – low pressure piston.
b) Compression in one stage – high pressure piston.
c) Two stages without intercooling.
d) Two stages with intercooling.
All of the circuits present the respective safety systems, relief valves, check valve such as two safety pressure switch.
The compression circuits are selected through the computer. The unit allows the representation of the instantaneous compressed cycle and the measurement of: the power consumed by the compressor, the data of pressure and temperature in every point of the compression and the operation time required to perform the compression.
This Computer Controlled Unit is supplied with the EDIBON Computer Control System (SCADA), and includes: The unit itself + a Control Interface Box + a Data Acquisition Board + Computer Control, Data Acquisition and Data Management Software Packages, for controlling the process and all parameters involved in the process.
ÜBUNGEN UND GEFÜHRTE PRAKTIKEN
GEFÜHRTE PRAKTISCHE ÜBUNGEN IM HANDBUCH ENTHALTEN
- Study of the compression process in a p-V diagram.
- Study of the work performed by a two-stage compressor.
- Determination of the efficiency of a two-stage compressor.
- Study of the pressure ratio and the temperature ratio of a two-stage compressor.
- Research on the relative behavior of the compressor for the electrical consumption, power of the shaft and heat losses, with and without intercooler.
- Research on the change of the volumetric efficiency against the compression ratio, with and without intercooling.
- Research on the change of the isothermal and/or polytrophic efficiency against the compression ratio, with and without intercooling.
- Research on the change of the mechanical performance against the compression ratio, with and without intercooling.
- Sensors calibration.
MEHR PRAKTISCHE ÜBUNGEN FÜR DAS GERÄT
- Study and analysis of the two-stage compression with intercooling by expansion.
- Study of the two-stage compression with intercooling by heat exchanger.
- Calculation of the inlet air dryness.
- Study of the design and function of a two-stage compressor.
- Determination of the intake air flow.
- Research on the change of the air flow against the pressure ratio, with and without intercooler.
- Study of the output power of the motor (power of the shaft of the compressor).
- Study of the cooling between stages effect on the compressor (power and temperatures of the cycle).
- Study of the two-stage compression effect and the interaction between stages on the energy requirements.
- Study of the single-stage compression with cooling by expansion.
- Study of the single-stage compression without cooling.
- Study of the single-stage compression with cooling by heat exchanger.
- Study of the heat balance in the heat exchanger.
- Sensors calibration.
Other possibilities to be done with this Unit:
- Many students view results simultaneously. To view all results in real time in the classroom by means of a projector or an electronic whiteboard.
- Open Control, Multicontrol and Real Time Control. This unit allows intrinsically and/or extrinsically to change the span, gains, proportional, integral, derivative parameters, etc, in real time.
- The Computer Control System with SCADA and PID Control allow a real industrial simulation.
- This unit is totally safe as uses mechanical, electrical and electronic, and software safety devices.
- This unit can be used for doing applied research.
- This unit can be used for giving training courses to Industries even to other Technical Education Institutions.
- Control of the HCDEC unit process through the control interface box without the computer.
- Visualization of all the sensors values used in the HCDEC unit process.
- By using PLC-PI additional 19 more exercises can be done.
- Several other exercises can be done and designed by the user.
ERGÄNZENDE AUSRÜSTUNG
Gerät für einen alternativen (reziprokierenden) Kompressor, computergesteuert (PC)
Gerät für kompressible Strömungen, computergesteuert (PC)
QUALITÄT
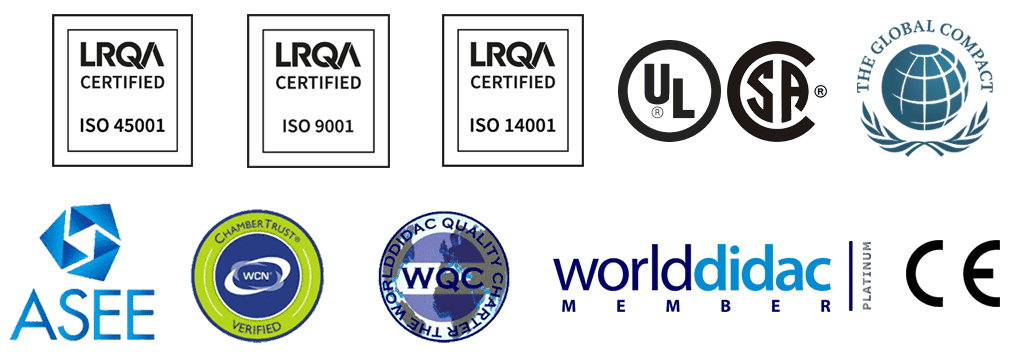
KUNDENDIENST
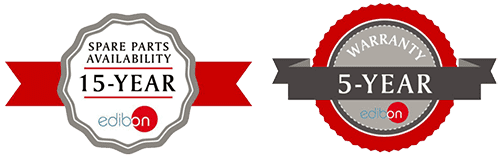