UDCC Gerät für kontinuierliche Destillation, computergesteuert (PC)
INNOVATIVE SYSTEME
The Computer Controlled Continuous Distillation Unit, "UDCC", designed by EDIBON, is a powerful laboratory tool for the study of variables affecting the distillation process.
Erweiterungen
Laboratorien
ÄHNLICHE NEUIGKEITEN
ALLGEMEINE BESCHREIBUNG
The Computer Controlled Continuous Distillation Unit, "UDCC", is basically composed by a boiler on which different types of interchangeable columns can be adapted (plate and filling (Raschig rings)). An eight plate column, a reflux system, a tank for distillation, a vacuum pump and a feeding pump (for continuous feeding) are included.
The steam that goes to the head of the column is sent to a total condenser. The cooling water flow that crosses the condenser is regulated and indicated in a flow sensor. Distillation can be carried out at low pressures with the help of an adjustable vacuum pump. The pressure loss in the column can be measured with a pressure sensor.
It allows continuous operation and batch operation.
For proceeding to continuous feeding, a pump that can inject the substance directly into the boiler or in any of the plates is available.
The temperatures of the system are measured by sensors placed in strategic positions.
This Computer Controlled Unit is supplied with the EDIBON Computer Control System (SCADA), and includes: The unit itself + a Control Interface Box + a Data Acquisition Board + Computer Control, Data Acquisition and Data Management Software Packages, for controlling the process and all parameters involved in the process.
ÜBUNGEN UND GEFÜHRTE PRAKTIKEN
GEFÜHRTE PRAKTISCHE ÜBUNGEN IM HANDBUCH ENTHALTEN
- Preparation of solutions.
- Analytic valuation techniques.
- Filling of the column.
- Batch operation. Continuous operation.
- Obtaining the McCabe-Thiele diagram. Without reflux.
- Obtaining the number of plates. Without reflux.
- Efficiency calculations. Without reflux.
- Variation of the composition of the distilled product: constant reflux ratio.
- Constant composition of the distilled product: variation of reflux ratio.
- Constant composition of the distilled product: constant reflux ratio.
- Continuos feeding of the column.
- Mass and energy balances across the system.
- Plates fluid dynamics studies, including load loss and column flooding.
- Study of the feed temperature effect on the continuos processes.
- Calculation of the theoretical number of floors in the plates columns, and the equivalent height of the theoretical floor (HEPT) in the Raschig rings columns.
- Pursuit of the temperatures in all plates in the column (Plates columns).
- Study of the rectification efficiency at different pressures.
- Effect of feed pre-heat.
- Effect of feed position.
- Demonstration of azeotropic distillation.
- Work different heating contribution with regulation by the computer.
- Studies of heating interchange in glass refrigerators.
MEHR PRAKTISCHE ÜBUNGEN FÜR DAS GERÄT
- Dosing pump calibration.
- Sensors calibration.
- Study of PID controls.
Other possibilities to be done with this Unit:
- Many students view results simultaneously. To view all results in real time in the classroom by means of a projector or an electronic whiteboard.
- Open Control, Multicontrol and Real Time Control. This unit allows intrinsically and/or extrinsically to change the span, gains, proportional, integral, derivative parameters, etc, in real time.
- The Computer Control System with SCADA and PID Control allow a real industrial simulation.
- This unit is totally safe as uses mechanical, electrical and electronic, and software safety devices.
- This unit can be used for doing applied research.
- This unit can be used for giving training courses to Industries even to other Technical Education Institutions.
- Control of the UDCC unit process through the control interface box without the computer.
- Visualization of all the sensors values used in the UDCC unit process.
- By using PLC-PI additional 19 more exercises can be done.
- Several other exercises can be done and designed by the user.
ÄHNLICHE VERFÜGBARE GERÄTE
Gerät für kontinuierliche Destillation
Gerät für diskontinuierliche Destillation
ERGÄNZENDE AUSRÜSTUNG
Destillation zur Rückgewinnung von Korrosiven Lösungsmitteln mit 4 l/h, computergesteuert und Touchscreen
Destillation zur Rückgewinnung von Korrosiven Lösungsmitteln mit 12 l/h, Gesteuert von PC und Touchscreen
Fortschrittliches Gerät für kontinuierliche Destillation, computergesteuert (PC)
Gerät für kontinuierliche Destillation
Gerät für diskontinuierliche Destillation, computergesteuert (PC)
Gerät für diskontinuierliche Destillation
Gerät für Crack-Säule, computergesteuert (PC)
QUALITÄT
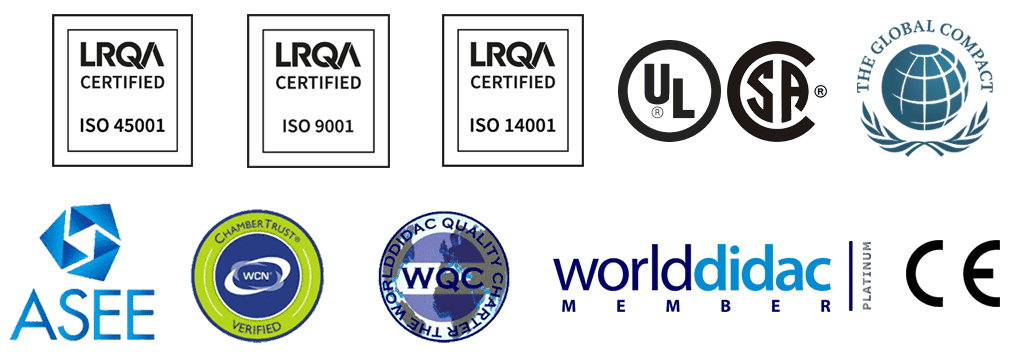
KUNDENDIENST
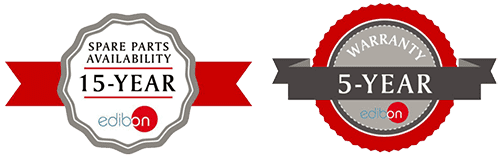