EDIBON Case study: "Development of Systems for Technical Training in the Process Control Field"
Development of Systems for Technical Training in the Process Control Field
Developing three modular systems to study metering systems and control algorithms, the tuning and testing of industrial controllers by the hardware-in-the-loop (HIL) simulation, and the analysis of real systems, such as industrial process control plants, through an architecture based on LabVIEW software with deterministic control hardware.
An important unit of the process control applications area is the Process Control Modular Unit (UCP), which studies instrumentation and measuring sensors as well as control algorithms and strategies used in industrial applications to control variables such as level, temperature, flow, pressure, pH, and more. Therefore, we developed control applications in the myRIO embedded system using the LabVIEW Real-Time Module, ECR (Figure 1). This allows for implementing systems for the acquisition and conditioning of sensors and transducer signals (thermocouples, piezoresistive sensors, capacitive sensors, and more) as well as for the control of actuators (pumps, solenoid valves, heating elements, and more) with control algorithms of the following types: PID, ON/OFF, feedforward, adaptative predictive control, fuzzy logic, and cascade control (Figure 2).
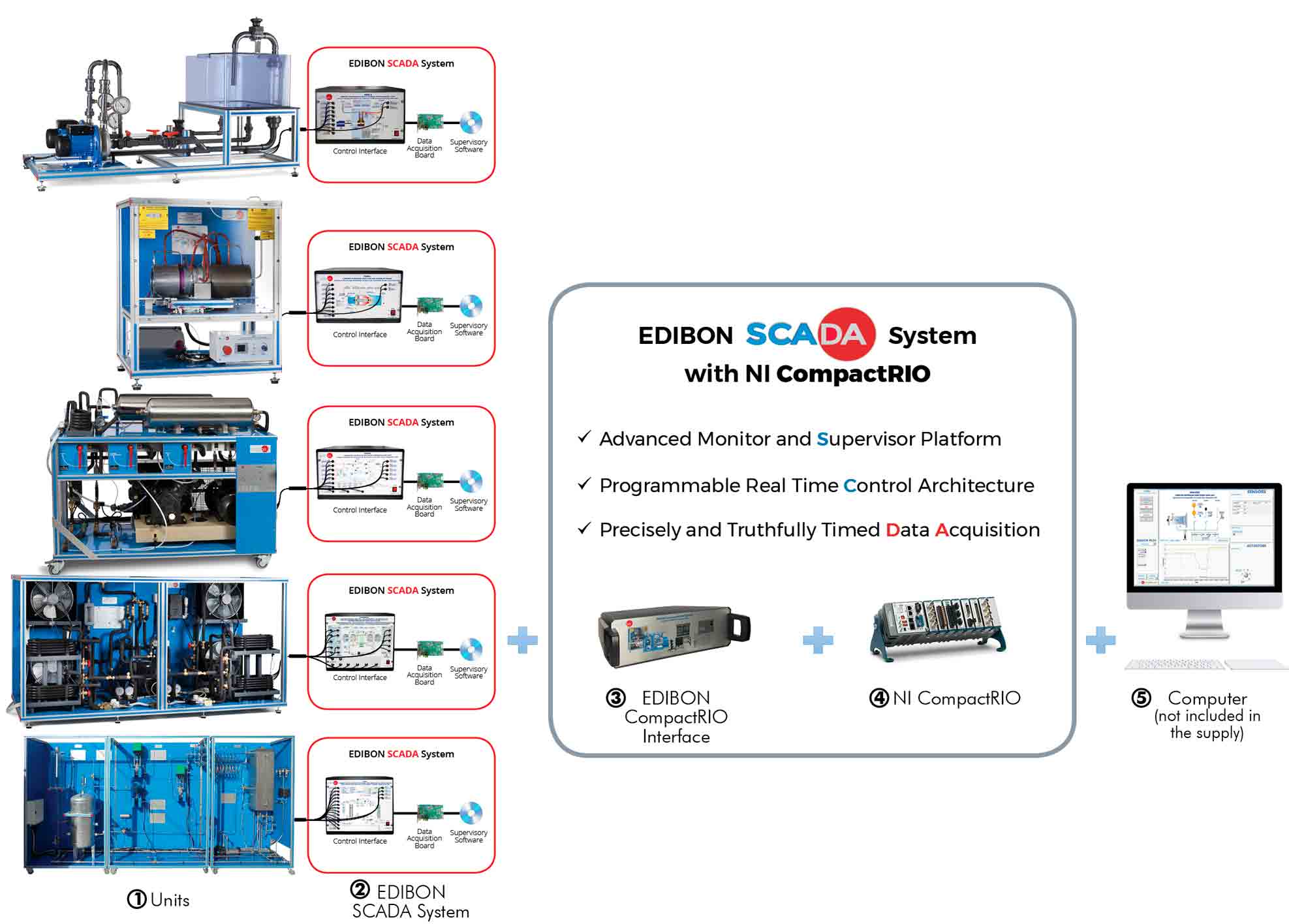
Figure 1. ECR. EDIBON Industrial Modular System with NI CompactRIO.
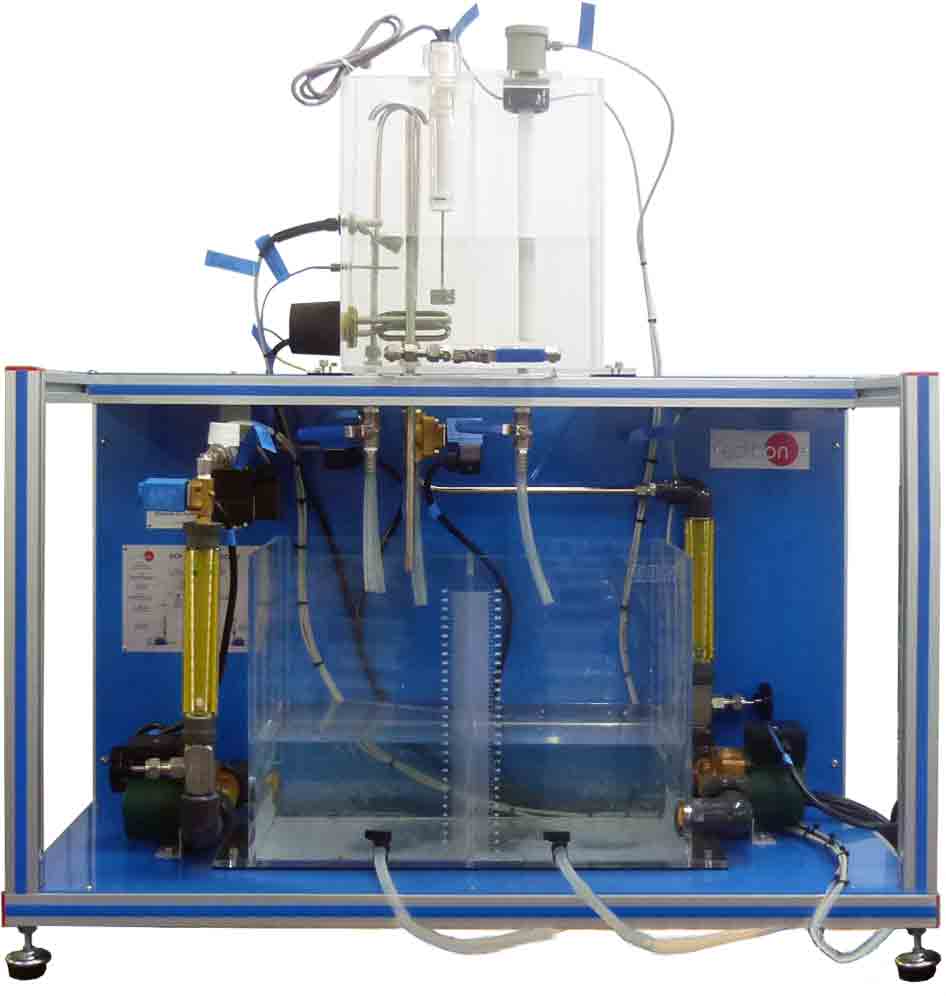
Figure 2. UCP (Computer Controlled Process Control Unit (Electronic Valve). A unit with complete Supervisory, Control and Acquisition Software for control it.
An important unit of the industrial systems process control area is the Process Control Plant with Industrial Instrumentation and Service Module (CPIC), a life-sized system of an industrial process control plant that includes all the elements commonly used in industry, such as water tanks, pressure vessels, pneumatic valves, analogical and digital sensors, pumps, and more. It also includes high-performance SCADA software. We recommend CompactRIO hardware to control those processes because it is more industrial and made up of both analog and digital I/O modules (NI 9209, NI 9263, and NI 9403). Combine CompactRIO hardware with LabVIEW Real-Time and the LabVIEW FPGA Module to develop a SCADA system for the control and monitoring of the process variables, implementation of optimized algorithms, event log, and alarms (Figure 3).
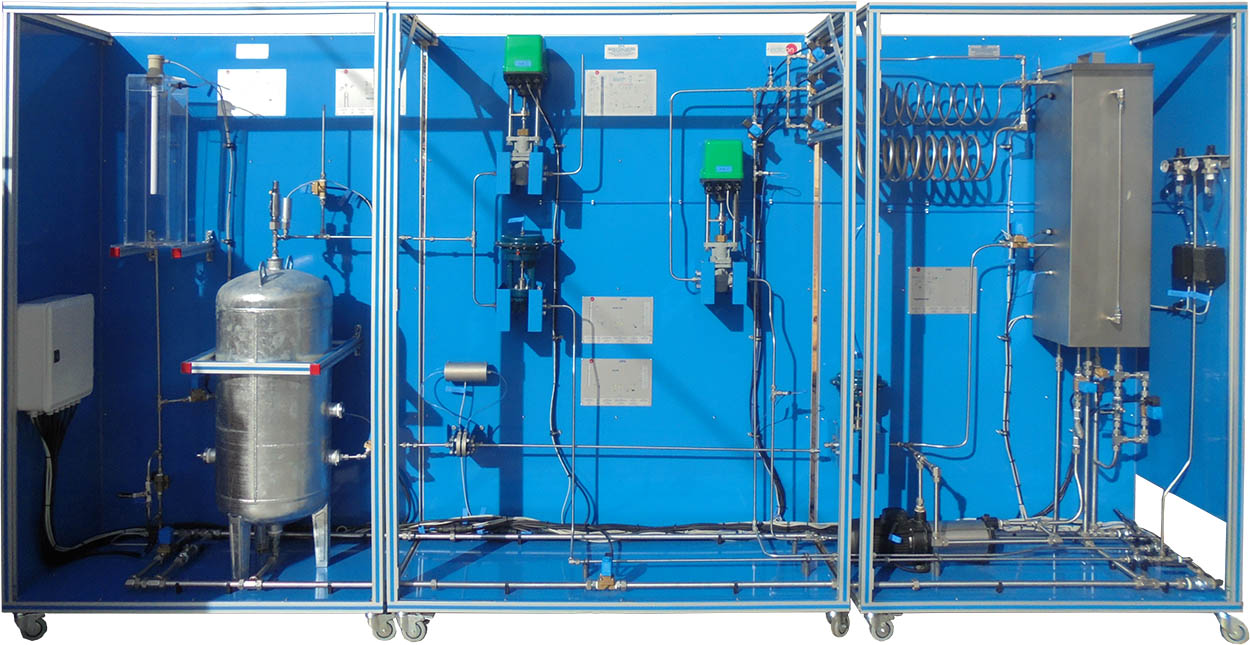
Figure 3.CPIC. Computer Controlled Industrial Process Control Plant.
Finally, an important unit in the controllers area is the Controller Tuning Trainer (CEAC), which implements one of the latest techniques for tuning and testing industrial controllers. It consists of simulating the process to be controlled in a hardware system, also known as hardware in the loop (HIL). This is possible thanks to the development of a SCADA application implemented in LabVIEW Real-Time that, apart from performing acquisition and control, simulates systems of different industrial processes in real time on a myRIO device (Figure 4).
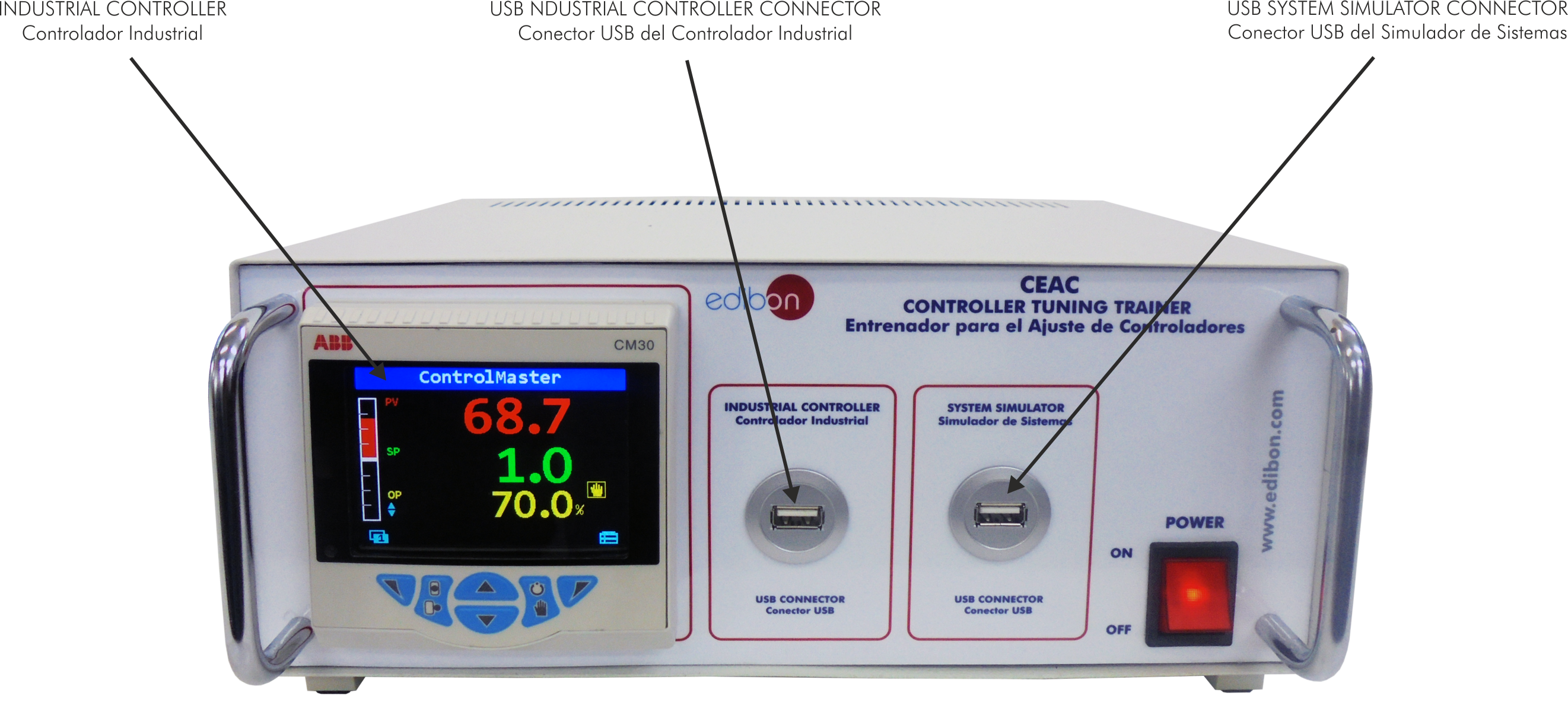
Figure 4.CEAC. Computer Controlled Controller Tuning Unit.
Two suplementary software packages accompany all the developments. The first one is the Interactive Computer Aided Instruction (ICAI) software system, which carries out practical exercises and tests with the units, assesses the users, obtains statistical results of their progress, and more (Figure 5a). The second one is the Software Development Kit (ELK) that gives the user a practical introductionto LabVIEW and helps the user access the source code and implement control algorithms centered on the Model-Based Design (MBD) methodology by the modelling and simulation of the systems to be controlled (Figure 5b).
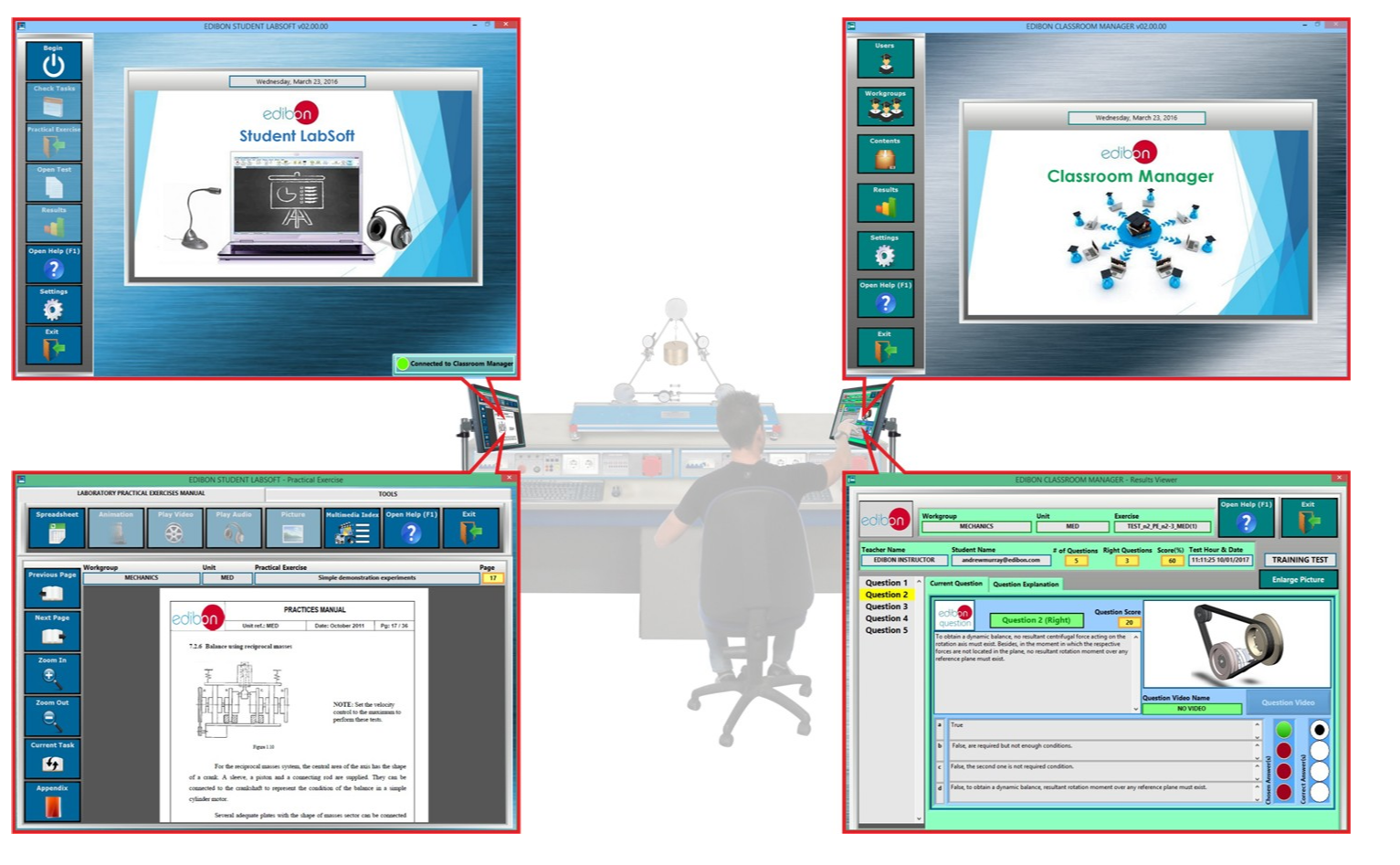
Figure 5(a).ICAI. Interactive Computer Aided Instruction Software
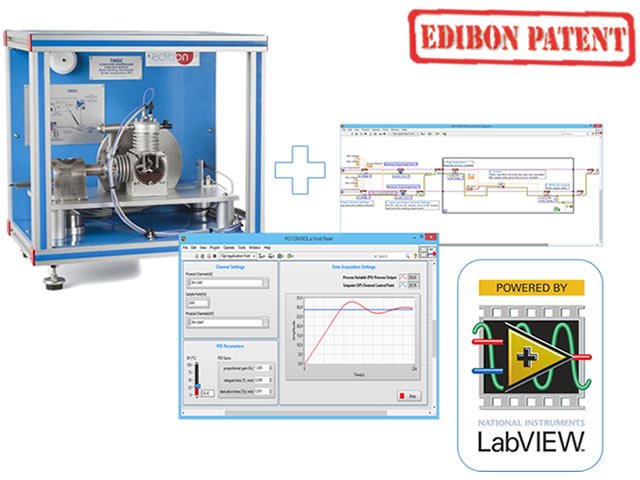
Figure 5(b). ELK, EDIBON Software Development KIT, Powered by NI LabVIEW™. Mechanics Toolkit of the Software Development Kit Based on LabVIEW.