UELLC Computer Controlled Liquid-Liquid Extraction Unit
INNOVATIVE SYSTEMS
The Computer Controlled Liquid-Liquid Extraction Unit, "UELLC", allows to study the extraction of one or several components in a continuous way with a solvent.
Expansions
Laboratories
RELATED NEWS
General Description
The Computer Controlled Liquid-Liquid Extraction Unit, "UELLC", is a laboratory scale unit designed to study the separation of the components of liquid mixtures by contact of the mixture with an immiscible solvent in which these components are preferentially soluble.
The extraction process is carried out in the glass liquid/liquid extraction column, which is composed of a jacketed glass packed column with two enlarged end sections. The joints between the three sections of the column are sealed with PTFE gaskets. The column is filled with glass Raschig rings that are supported on a perforated PVC plate.
Feed for the column is stored in the feeding tank from where it is pumped by a computer controlled diaphragm pump. It passes through a flowmeter and enters the base section of the column via an injector mounted on it. Refine (phase with low content of solute) leaves the top of the column through a pipe and is collected in a refined tank.
The solvent supply tank provides the feed for a computer controlled diaphragm pump. The solvent is pumped and passes through a flowmeter, then enters the top of the column via an injector. Extract (phase with high content of solute) leaves the bottom of the column through a pipe and is collected in an extract tank. A drain valve is fitted in the extract line.
The supply circuits and product collection circuits include two pressure switches that switch off the pumps when the pressure is high, two sampling taps to collect samples, three-way directional valves to direct the different currents and a regulation valve to control the height of the interface.
The distillation process is carried out in the distillation column boiler. The distillation column is made up of a glass section and contains Raschig rings made of glass. It is mounted close to the extraction column and fitted at such a height that the solute may be drained into the solute tank.
Heating is done by means of a computer controlled heating mantle (with control of the temperature in the column head) in the base of the boiler and the boiler temperature is indicated on a temperature sensor. The boiler lid is perforated where the distillation column is fitted and a pipeline allows to drain the extract from the extract tank. The boiler-solute tank circuit includes a sampling tap to collect samples.
The dissolvent vapor phase is condensed in the coolant column and re-cycled to the solvent tank to recover the dissolvent and to provide a closed circuit. Then, the solvent can be re-cycled continuously.
All storage tanks have force sensors to measure the mass in the five tanks (feed, refined, solvent, extract and solute) and to calculate the liquid volume.
This Computer Controlled Unit is supplied with the EDIBON Computer Control System (SCADA), and includes: The unit itself + a Control Interface Box + a Data Acquisition Board + Computer Control, Data Acquisition and Data Management Software Packages, for controlling the process and all parameters involved in the process.
Exercises and guided practices
GUIDED PRACTICAL EXERCISES INCLUDED IN THE MANUAL
- Preparation of acid–base titration of the feed.
- Obtaining of the binodal curve.
- Study of theoretical and experimental mass balances.
- Calculation of the flooding velocity of the extraction column.
- Regulation of the height of the interface in the extraction column.
- Determination of the critical point existence.
- Study of the effect of the temperature in the liquid-liquid extraction process.
- Calculation of the mass transfer volumetric coefficient, referred to the continuous phase.
- Study of the efficiency of the extraction.
- Study of the batch operation regarding the solvent or the supply.
- Study of the extraction process for industrial processes.
- Calculation of the solvent recovery effectiveness.
- Study of the distillation process control.
- Repetition of the previous practical exercises for different compounds.
- Calibration of the pumps.
- Sensors calibration.
MORE PRACTICAL EXERCISES TO BE DONE WITH THE UNIT
- Many students view results simultaneously. To view all results in real time in the classroom by means of a projector or an electronic whiteboard.
- Open Control, Multicontrol and Real Time Control. This unit allows intrinsically and/or extrinsically to change the span, gains, proportional, integral, derivative parameters, etc, in real time.
- The Computer Control System with SCADA and PID Control allow a real industrial simulation.
- This unit is totally safe as uses mechanical, electrical and electronic, and software safety devices.
- This unit can be used for doing applied research.
- This unit can be used for giving training courses to Industries even to other Technical Education Institutions.
- Control of the UELLC unit process through the control interface box without the computer.
- Visualization of all the sensors values used in the UELLC unit process.
- By using PLC-PI additional 19 more exercises can be done.
- Several other exercises can be done and designed by the user.
SIMILAR UNITS AVAILABLE
SUPPLEMENTARY EQUIPMENT
Liquid-Liquid Extraction Unit
Computer Controlled and Touch Screen Solid-Liquid Extraction Pilot Plant
Computer Controlled Solid-Liquid Extraction Unit
Solid-Liquid Extraction Unit
Computer Controlled Batch Solvent Extraction and Desolventising Unit
Computer Controlled Unit to Study Flow through Packed Columns
Quality
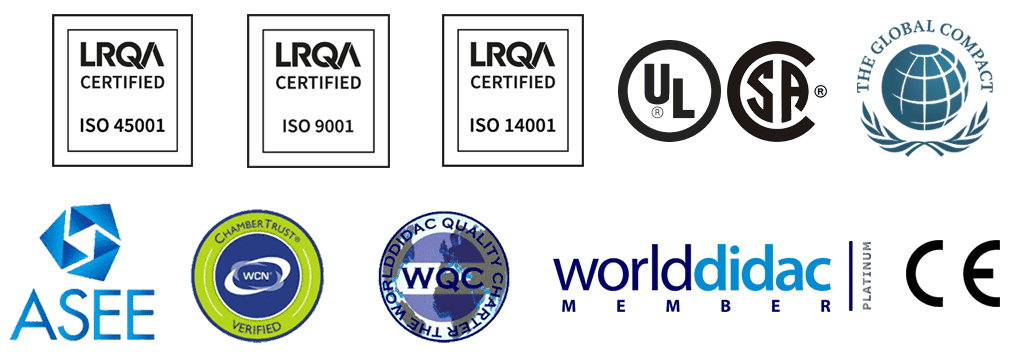
AFTER-SALES SERVICE
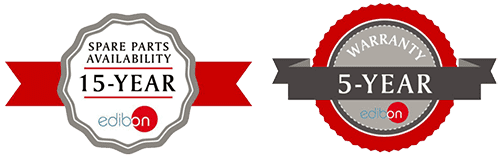